Celebrating 40 Years of
Cutting-Edge Solutions
The Mabarex Approach
Celebrating 40 Years of Cutting-Edge Solutions
01
Understanding
Analyzing
02
Designing
Optimizing
03
Implementing
Operating
Our Trusted Partners
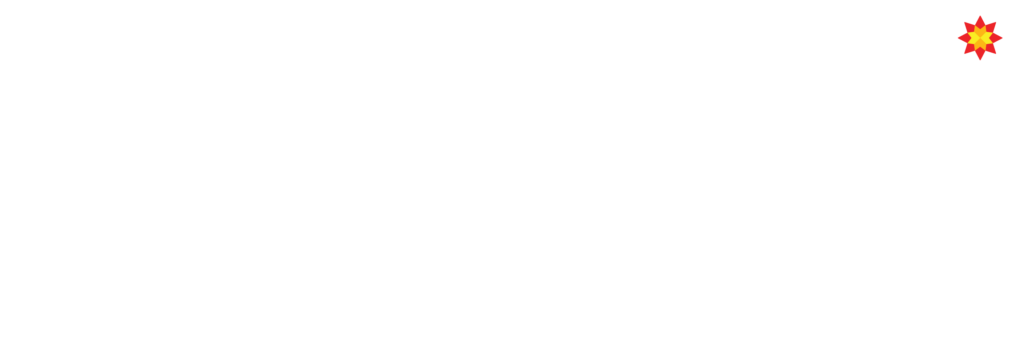
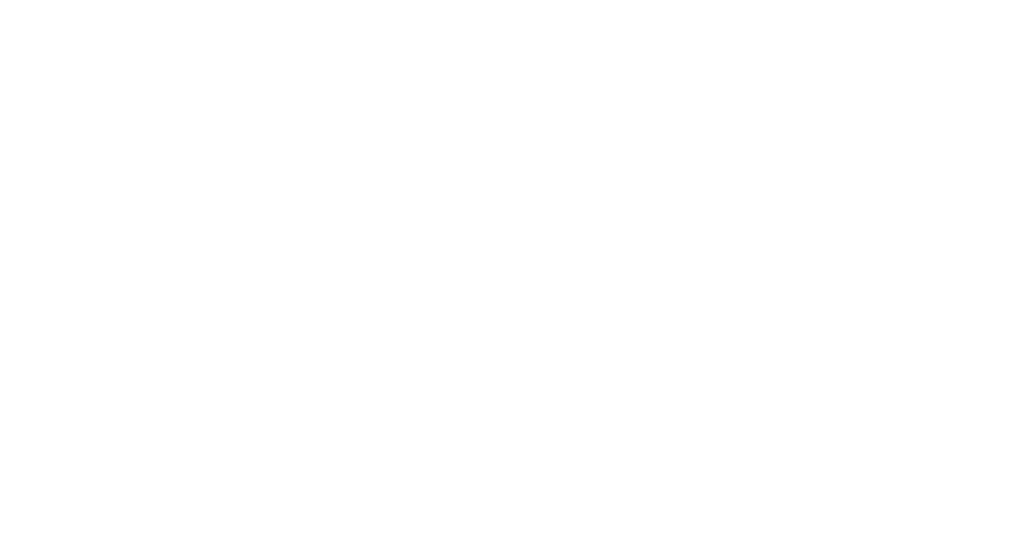
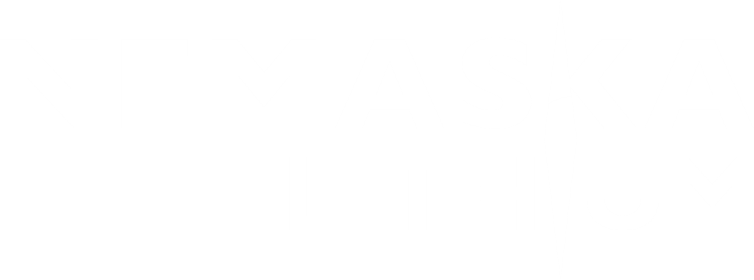
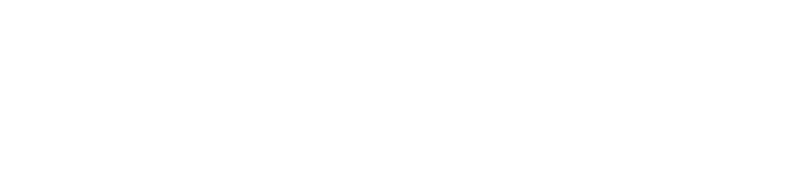
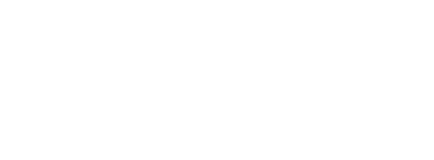
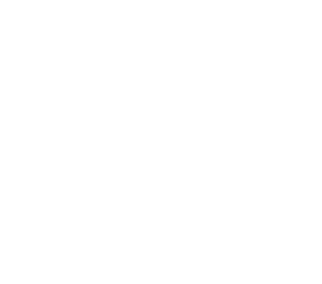
Our team of experts
We take pride in our commitment to making a positive impact on the environment.
Our Products
Our Services
Nos produits
Nos alliances stratégiques avec des partenaires de qualité nous permettent d’offrir des solutions de traitement d’eau efficaces, robustes et fiables et ce, pour tous types d’application et tailles de projet. Les technologies et notre savoir sont nos outils! L’important pour nous, est de vous offrir la solution qui répond le mieux à vos besoins spécifiques peu importe si c’est en utilisant une de nos technologies exclusives ou celle d’un partenaire.
Nos services
Notre équipe d’experts peut vous accompagner lors de toutes les étapes de votre projet. De la phase d’étude préliminaire, en passant par les phases de conception et de réalisation, jusqu’à la mise en route et l’opération d’usines performantes de traitement des eaux. La dispersion géographique de nos techniciens tout comme notre service de suivi et d’accompagnement à distance assurent une présence sécurisante et permet une intervation rapide et efficace.
Our Achievements
Take a closer look at what MABAREX can do for you by consulting our most recent projects. Whatever the size of your project or sector in which your organization operates, our team is there to support you in achieving your objectives.
For 40 years, we have been offering increasingly complete and complex water treatment solutions, which makes us today a company recognized for our innovation. The interaction and teamwork between the different members of the team means that we move forward as one towards a common goal, the protection of the environment. 1,500 projects completed, 4 continents covered and 200 million m3 of treatment capacity added over the past 40 years.
MABAREX celebrates its 40th anniversary and remains a pioneer by carrying out the first PFAS (forever pollutants) treatment project in Quebec.
40 years of expertise
CESM (complexe environnemental de Saint-Michel): a unique sorting centre in the heart of the city
Latest News
Actualité
Chez MABAREX nous nous démarquons par notre approche humaine, centrée sur votre contexte unique, mais aussi sur notre capacité à vous offrir des solutions intégrées combinant les meilleures technologies disponibles. Apprenez-en plus sur le traitement des eaux et les différentes solutions qui s’offrent à vous en consultant nos dernières actualités.
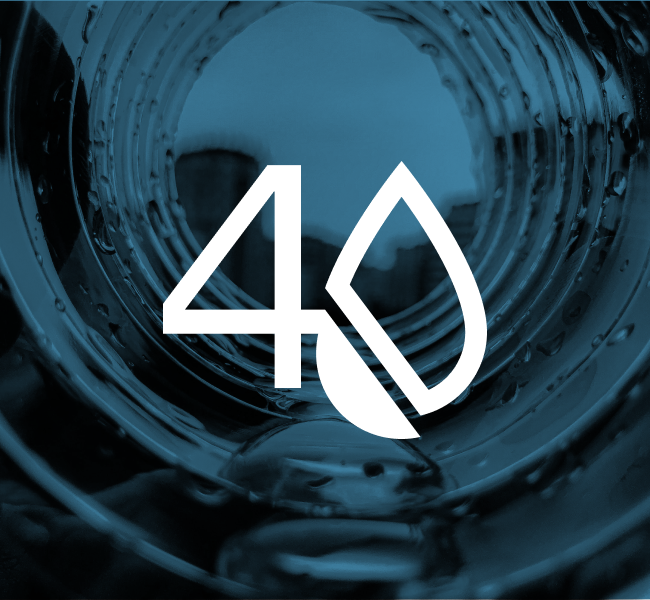